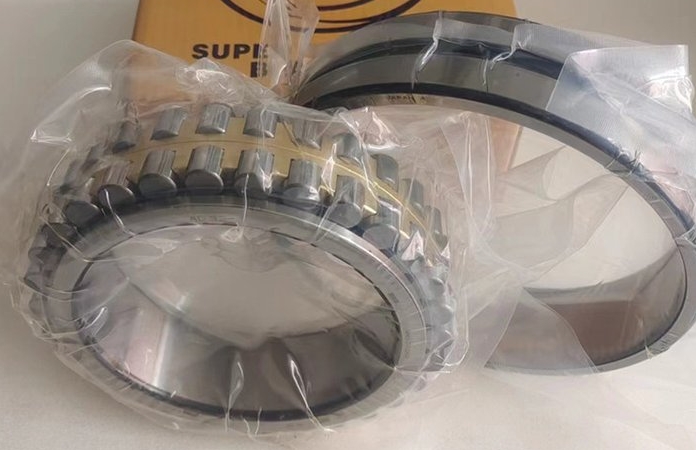
从上述失效特征来看,轴承滚子出现了严重偏差,导致滚子端面、保持架凹穴、外圈护边磨损,内圈疲劳剥落和高温二次淬火现象。近年来,这类轴承经常会发生类似故障,具有外圈挡边严重磨损、滚子端面严重磨损、内外滚道接触疲劳剥落等故障特征。
当轴承高速运转时,如果有任何微小的干涉或变化(如高温引起的润滑油碳粒),高速滚子会产生动态不稳定、摆动,结果会导致滚子端面和外圈护罩之间出现异常滑动磨损,滚子的外表面也会在内圈滚道的表面上滑动。最终导致与之接触的保持架凹穴内表面滑动或磨损,一系列的滑动和磨损将伴随着温度的升高,随着时间的推移,磨损和温升会增加,直到轴承失效。
导致辊子动态不稳定和侧摆的主要因素如下,一是滚子精度,主要包括辊子直线段的直线度、圆弧斜率和倒角的对称性、直径差和长度差、辊子端面的平行差和垂直差、表面粗糙度等,二是套圈滚道的平直度,三是外圈护边平行差,四是保持架袋孔精度,主要包括梁与边梁的竖向差异、底部至保持架端壁厚度差异等,四是滚筒端面与外圈护罩之间的间隙,五是异物干扰。
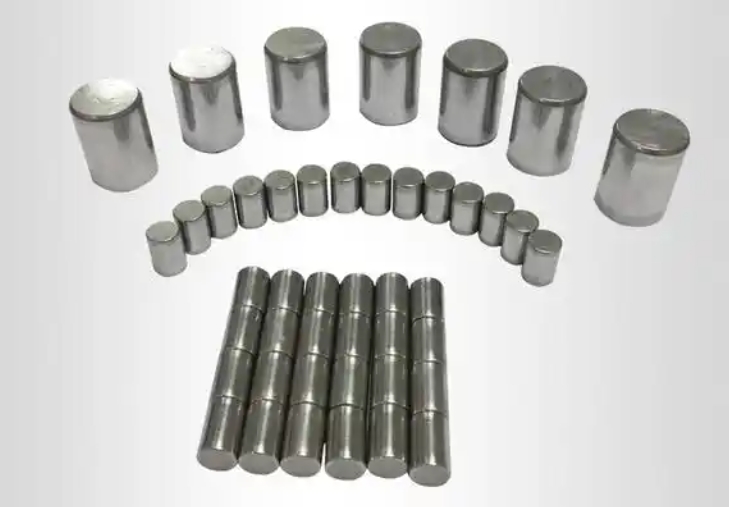
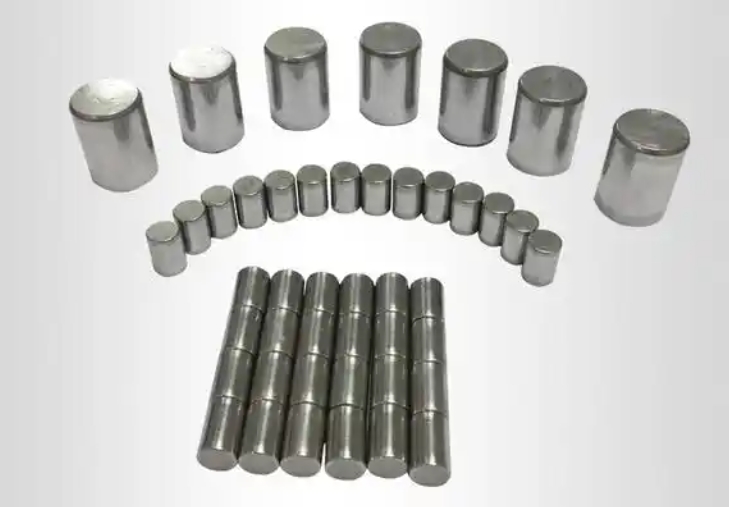
如果轧辊精度不好,将直接影响轧辊在高速轧制条件下的动平衡,从而破坏轧辊的运行稳定性,在辊子动态失稳的早期阶段,如果外圈防护罩的平行差、环形滚道和保持架孔的直线度等精度足够高,将对辊子的动态失稳起到约束作用,从而使其保持在正常运行状态。
否则,将增加辊子的动态不稳定性,当滚子和套圈的边缘以非常高的转速发生滑动摩擦时,摩擦热也很高,此时,如果滚子端面与套圈轮缘之间的间隙过小,则难以形成润滑油膜,冷却效果将受到严重影响,最终导致滚子端面和套圈轮缘的高温磨损。
否则,将增加辊子的动态不稳定性,当滚子和套圈的边缘以非常高的转速发生滑动摩擦时,摩擦热也很高,此时,如果滚子端面与套圈轮缘之间的间隙过小,则难以形成润滑油膜,冷却效果将受到严重影响,最终导致滚子端面和套圈轮缘的高温磨损。
通过轮廓仪对故障轴承套圈的滚道和滚子的直线度进行了测试,确认各部分的原始直线度符合要求,可以消除这一因素的影响,通过设计审查,发现辊子长度差要求低,弧形斜面为磨削表面,粗糙度和精度低,外圈保持边缘的基准端面的平行差也要求较低,这些因素应该是影响轴承滚子高速旋转时动态稳定性的主要因素。
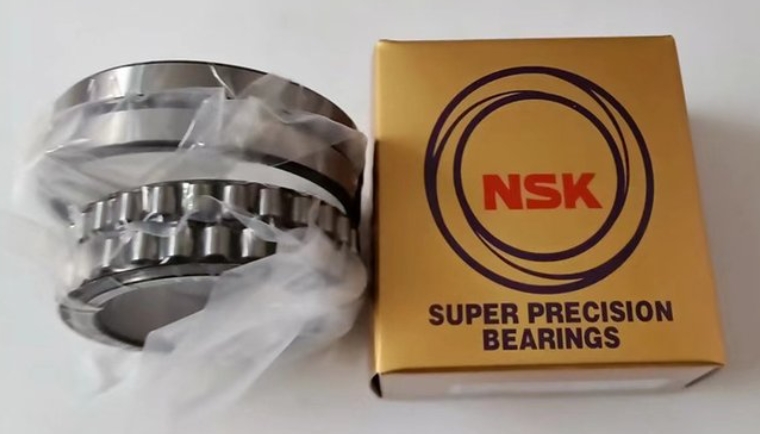
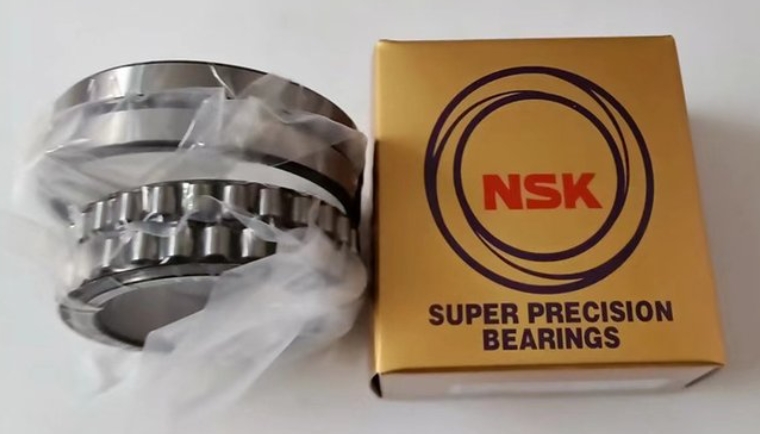
根据故障原因分析结果,以下技术改进措施可以有效改善遇到的问题,一是外圈护边与基准端面的平行差从5m增加到3m,二是将每组辊子的长度差从8m增加到4m,直径差从0.7131增加到0.5m,三是增加保持架袋孔底部保持架端壁厚度差的要求(不超过0.05mm),四是增加辊子两侧弧形斜面的超精加工要求,五是增加测量滚筒端面与外圈护罩间隙的要求。
这些改进措施有效地提高了辊子高速旋转时的动态稳定性,大大提高了后期生产中轴承的质量,从而提高了轴承的寿命和可靠性,保证了主机的安全。